Print #0 - my first minimug. Nearly perfect. :)
Used the ready-made Gcode from BfB and no
changes to temperature or extrusion rate
even though I used colored ABS that usually
is said to require 2-4°C higher temperatures.
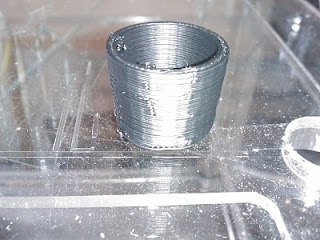
Print #1
A belt clip using the standard-settings from the Wiki.
The infill does not reach the shell.
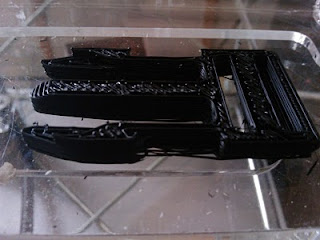
Print #2:
Better infill, only 1 raft-layer.
There was so much warping that the tool-head pushed
the object around by colliding with already printed layers.
Reaction: Lowered the height-over-width ratio of raft+interface layer,
so it would push the fillament more only the build-platform, so it would
stick better.
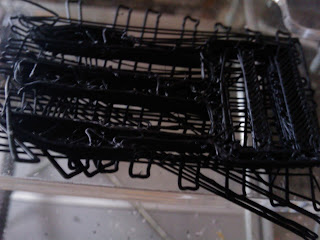
print #3:
OK, the head is MUCH higher then before.
Aparently I was supposed to give a higher
value for thie setting instead of a lower one.